Chakli Machine
Product Description:
The Chakli Machine generally consists of a hopper to hold the dough, a handle or motor to operate the extrusion process, and multiple discs with different patterns for shaping the chakli. Some models may be manual, where the user applies pressure to the dough, while others are electric, making the process faster and more convenient. These machines are particularly useful for large-scale preparation, such as during festivals or family gatherings, and can help save time and effort.
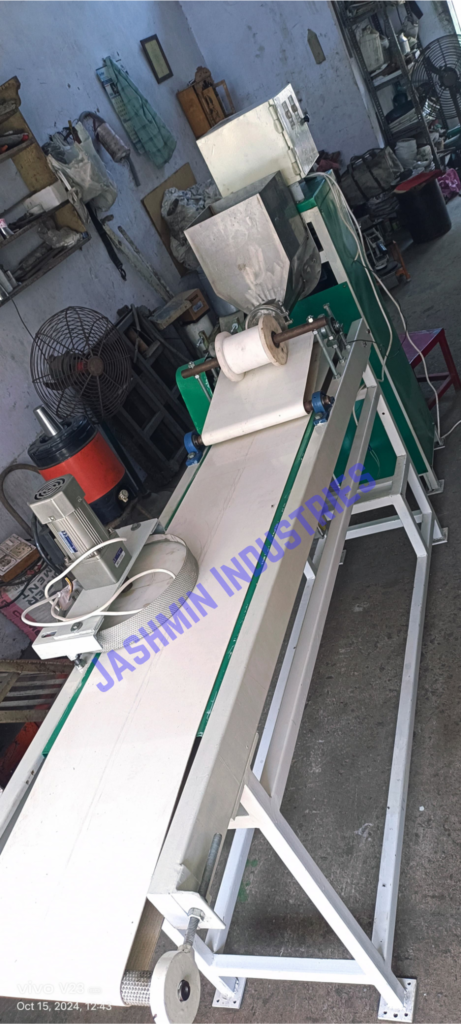

Benefits of Automatic Chakli Machine
High Efficiency:
Produces a large quantity of chaklis in less time, making it ideal for businesses with high production demands.
Consistent Quality:
Ensures uniform size, shape, and texture of chaklis, enhancing product appeal.
Ease of Operation:
Simple to operate with minimal training, reducing the need for skilled labor.
Time-Saving:
Automates the manual process, significantly reducing the production time.
Hygienic Production:
Minimizes human contact with food, ensuring better hygiene and compliance with food safety standards.
Cost-Effective:
Lowers labor costs and increases production capacity, offering a better return on investment.
Durability and Reliability:
Made from high-quality materials, ensuring long-term usage with minimal maintenance.
Versatile Usage:
Can be used to produce various snacks besides chakli, adding flexibility to operations.
Energy-Efficient:
Designed to consume less power, making it environmentally friendly and economical.
Customization Options:
Offers adjustable settings for size and design, catering to diverse customer preferences.
Jashmin Industries Leading Manufacturer of Chakli Machines in India
We are Jashmin Industries, a trusted name in the food processing industry, specializing in the manufacturing of high-quality Chakli Machines. We offer a wide range of automatic and semi-automatic chakli-making machines designed to meet the growing demands of the snack industry. Our machines are engineered with precision to ensure consistent shape, size, and texture of chaklis, making them ideal for commercial use.
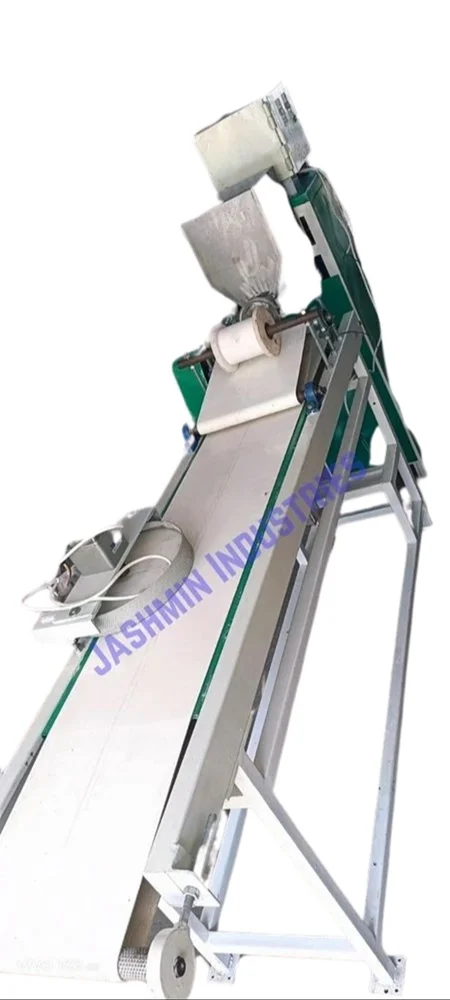
Our Range of Chakli Machines
- Automatic Chakli Machine – High-speed production with minimal manual effort.
- Semi-Automatic Chakli Machine – Perfect balance of automation and control.
- Industrial Chakli Making Machine – Designed for large-scale production with enhanced efficiency.
Why Choose Jashmin Industries for Chakli Machines?
✅ High Production Capacity: Our machines deliver high output to meet bulk requirements.
✅ Durable and Robust Design: Built with stainless steel for longevity and hygiene.
✅ Easy to Operate and Maintain: User-friendly interface and low maintenance cost.
✅ Customizable Options: Tailored solutions to fit your production needs.
Industries We Serve
Our Chakli Machines are ideal for:
- Food Processing Units
- Snack Manufacturers
- Small and Medium Enterprises (SMEs)
- Commercial Kitchens
Technical Specifications
- Power-efficient and cost-effective operations
- Consistent and uniform chakli shapes
- Multiple die options for various designs
Contact Us
Partner with Jashmin Industries +91 9825641435 to enhance your snack production with our innovative and reliable Chakli Machines. For inquiries and quotes, contact us today!